The Custom Metal 3D Printing Design Process
- quickparts14
- Mar 24
- 3 min read
In today's rapidly evolving manufacturing landscape, custom metal 3D printing has emerged as a transformative technology that allows for the production of intricate and tailored parts with unprecedented efficiency. Whether you are an engineer, a designer, or an innovative entrepreneur, understanding the design process for custom metal 3D printing is essential to turn your concepts into reality. We will outline the step-by-step process of designing for custom metal 3D printing of your projects.
Step 1: Ideation and Concept Development
The first step in the custom metal 3D printing design process begins with coming up with ideas. This phase involves identifying the specific needs of your project and clearly defining the functionality of the part you intend to create. Consider questions such as:
What is the primary function of the part?
Are there specific performance requirements, such as weight limits or temperature thresholds?
Who is the target audience or market for your design?
The next steps in the planning process will be guided by how well you can explain your idea and how you want to use it.
Step 2: Creating CAD Models
Once you have a clear concept in mind, the next step is to create a Computer-Aided Design (CAD) model. You can use this model as a starting point for your custom metal 3D printing project. When creating your CAD model, consider the following points:
Design for Additive Manufacturing (DfAM): Custom metal 3D printing allows for complex geometries that traditional manufacturing methods cannot achieve. Use this to your benefit by adding internal pathways, organic forms, and lattice structures. But watch out for extensions and other elements that can make printing more difficult.
Consider Tolerances: Ensure that you set appropriate tolerances in your design. Metal 3D printing often requires tighter tolerances than other methods, as parts may experience thermal expansion or contraction during printing. Working within the guidelines provided by your 3D printing service can help reduce the risk of errors.
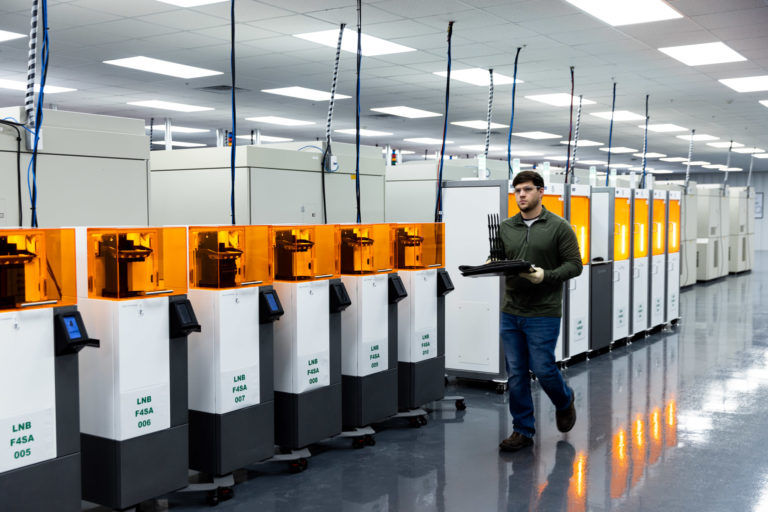
Step 3: Material Selection
Choosing the right material is crucial for the success of your custom metal 3d printing project. Different metals have unique properties that can significantly affect the performance of your final product. Here are a few factors to consider during material selection:
Mechanical Properties: Assess the mechanical requirements of your part. For example, titanium is known for its strength-to-weight ratio, making it ideal for aerospace applications, while stainless steel is favored for its corrosion resistance and durability in various conditions.
Thermal and Electrical Conductivity: Thermal and electrical conductivity may be very important depending on the use. Copper is a good conductor, but it can be hard to print on. Aluminum, on the other hand, has an excellent combination of qualities that make it useful in many situations.
Compatibility with 3D Printing: Some materials may not be suitable for certain printing technologies. Ensure that the chosen material is compatible with the metal 3D printing process you intend to use.
Step 4: Prototyping and Iteration
Before moving to production, it's essential to create a prototype to evaluate the design and functionality of your part. Rapid prototyping allows for quick iterations and testing, helping to identify potential flaws or areas for improvement. Here are some best practices for successful prototyping:
Print a Test Version: Consider using less expensive materials or simpler methods for your initial prototypes. This step will allow you to test fit and form without incurring high costs.
Conduct Tests and Analysis: Once you have a prototype, conduct performance tests to evaluate its properties against the design requirements. Is it strong enough? Does it fit as intended? Gathering data here is crucial for making necessary adjustments.
Request Feedback: Engage stakeholders and potential users for their opinions on the prototype. Based on this feedback, design changes may be made that are better.
Step 5: Final Adjustments and Production
After prototyping and testing, it’s time to refine your design based on the evaluation you’ve gathered. This may involve tweaking proportions, altering geometries, or even changing materials if necessary.
Once you are confident that your design meets all criteria, prepare it for production. This phase includes generating the final slicing files required to guide the 3D printer, and ensuring all settings are improved for the chosen material and technology.
By following the outlined steps you can optimize your design process and achieve successful outcomes for your projects.
Comentarios